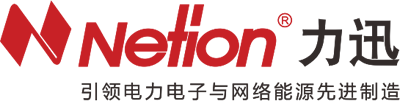
广东力迅电力电子科技有限公司,衷心期待着与您的合作!
地址:广东.三水.三水大道南62号
电话:0757-87360282,0757-87380181,8008305182
传真:0757-87360189
邮箱:business@netion.com.cn

扫一扫,关注我们
NETION NEWS
力迅动态近日,经过严格的初审、终审厂验,反复的工艺和参数的对比和现场测试,以及对性价比、服务简便性、整体服务流程的可行性细致筛选,结合样品在现场使用状况的评比,力迅订制的工业级UPS方案,成功服务于航天某部制造基地,随着一批批订制设备的正式投入使用,力迅CPG系列300-600kVA工业级UPS将为其精密设备和仪器提供可靠的电力保障,确保其精密制造设备长期稳定运行。力迅专注电源、电力电子及新能源电力转换领域事业近30年,将以此为契机,为中国高端制造业的崛起做出力所能及的贡献。
火箭发动机壳体也是导弹壳体,它的工作环境极为恶劣,包括发动机工作产生的高温、高速飞行产生的气流冲击、温度聚然变化、对方反导拦截武器攻击等等。因此要求发动机壳体具备良好的耐高温、耐腐蚀、强度高、抗冲击等方面性能。
早期火箭发动机多采用金属壳体,例如超高强度钢、钛合金等,但是金属材料重量大,影响射程和载荷,因此火箭发动机壳体发展趋势就是采用高强度非金属材料。
起初主要采用玻璃纤维、芳纶、石墨等,在相同尺寸下,发动机壳体质量可以减少50%左右,战略导弹投掷重量可以提高1倍以上,可以说效果非常明显。
不过这类材料在强度、刚度等方面还存在一定缺陷,因此上世纪80年代之后,碳纤维开始在固体发动机壳体上面得到运用。
碳纤维与芳纶相比,刚度和强度可以提高80%和30%,壳体重量再一次下降40%,另外碳纤维壳体热膨胀系数小,发动机工作期间尺寸稳定,可以提高发动机工作可靠性。
与金属材料制造火箭发动机外壳工艺相比,新材料虽然质地柔软,但是制造的火箭发动机外壳强度、韧性并不低,是金属的数倍,且可承受火箭飞行过程中产生的高温等极端情况影响。
进入新世纪,随着国产碳纤维水平突飞猛进,T800级碳纤维已经实现1000吨级生产能力,T1000也达到100吨级。
伴随我国M60J级碳纤维研制成功,这表明国产碳纤维在三个重要方向(高强高模量、高强度、高模量)都实现了突破,从而为碳纤维在国产导弹和运载火箭上面运用打下了坚实的基础。
在国产200吨推力固体火箭发动机采用了多项先进技术这中有一项最为引人注目,那就是大直径碳纤维缠绕复合材料壳体技术,标志着中国已经掌握大型固体火箭发动机碳纤维缠绕复合材料壳体技术。
将一缕宽约1厘米的黑色碳纤维“线束”,在特定装置上一层一层多次叠加缠绕,并浸染上特殊树脂,经高温固化,再采用先进的热处理和表面处理技术,提高碳纤维外壳的耐高温性能和抗氧化能力,火箭发动机的外壳便初步成型。
用精密的缠绕数控机床,来严格控制碳纤维的缠绕速度和张力,确保每一层碳纤维都紧密贴合,形成坚固的外壳。
本案配置亮点:
●输入输出全隔离,突载、干扰、零地问题得到根本解决,同时,设备和人员安全也得到高级别保障。
●抗冲击能力强,对于反复启停的感性负载适应性超强。
●过载能力大幅提升,200%负载运行10分钟。
●防护等级达到IP54,具有超强的环境适应能力,如高温(65℃以下)、高湿、粉尘、震动等。
●内部元器件防尘处理,同时使用三防漆工艺,可以防止酸碱侵蚀,提高了产品的可靠性。
●内部元器件均做了特别的防油脂处理,进一步提高了对现场环境的适应能力。
●结构模块化,元器件安放于密闭的装置里,维护简便快捷。
●授权后,多个参数可调,可控性强。
●调速智能风机,风量大风速自然,更换方便。
●完美的高频静音技术,工作环境无忧。
●输入功率因素高达95%,节能高效,大大为用户节约使用成本。
●超高精度输出:额定值精度<±0.5V;设备启停瞬时变化值<±2V,响应恢复时间<2ms。
地址:广东.三水.三水大道南62号
电话:0757-87360282,0757-87380181,8008305182
传真:0757-87360189
邮箱:business@netion.com.cn
扫一扫,关注我们
Copyright © 2022 广东力迅电力电子科技有限公司 版权所有 粤ICP备09114476号 粤公网安备44060702000178号