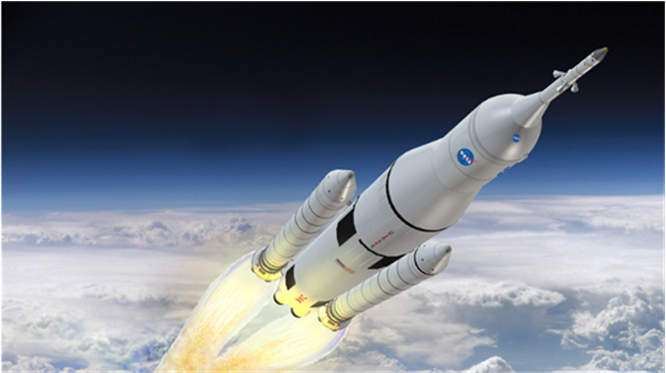
Recently, after strict initial and final factory inspections, repeated comparisons of processes and
parameters, and on-site testing, as well as careful screening of cost-effectiveness, service simplicity, and overall service process feasibility, combined with the evaluation
of sample usage on site, the industrial UPS solution customized by Netion has successfully served a
manufacturing base in a certain aerospace department. With the formal use of batches of customized
equipment, Netion CPG series 300-600kVA industrial UPS will provide reliable power guarantee for
its precision equipment and instruments, ensuring the long-term stable operation of its precision
manufacturing equipment. Netion has been focusing on the
fields of power supply, power electronics, and new energy power conversion for nearly 30 years, and
will take this as an opportunity to contribute to the rise of China's high-end manufacturing industry
to the best of its ability.
The shell of a rocket engine is also a missile shell, and its working environment is extremely harsh,
including high temperatures generated by engine operation, airflow impacts generated by high-speed flight, temperature fluctuations, and attacks from enemy anti missile interception weapons.
Therefore, it is required that the engine housing has good performance in high temperature resistance,
corrosion resistance, high strength, impact resistance, and other aspects.
Early rocket engines often used metal shells, such as ultra-high strength steel, titanium alloys, etc. However, the heavy weight of metal materials affected the
range and load, so the development trend of rocket engine shells is to use high-strength non-metallic
materials.
At first, glass fiber, aramid, graphite, and other materials were mainly used. Under the same size, the
weight of the engine housing can be reduced by about 50%, and the weight of strategic missile
throwing can be increased by more than twice. It can be said that the effect is very significant.
However, these materials still have certain defects in strength, stiffness, and other aspects. Therefore,
after the 1980s, carbon fiber began to be used in solid engine casings.
Compared with aramid, carbon fiber can increase stiffness and strength by 80% and 30%, respectively,
while reducing the weight of the shell by another 40%. In addition, carbon fiber shell has a smaller
coefficient of thermal expansion, ensuring stable dimensions during engine operation and improving
engine reliability.
Compared with the process of manufacturing rocket engine shells using metal materials, although
the new material has a soft texture, the strength and toughness of the rocket engine shell produced
are not low, several times that of metal, and can withstand extreme conditions such as high
temperatures generated during rocket flight.
In the new century, with the rapid development of domestic carbon fiber level, T800 grade carbon
fiber has achieved a production capacity of 1000 tons, and T1000 has also reached 100 tons.
With the successful development of M60J carbon fiber in China, it indicates that domestic carbon
fiber has achieved breakthroughs in three important directions (high strength and high modulus,
high strength, and high modulus), laying a solid foundation for the application of carbon fiber in
domestic missiles and launch vehicles.
The domestically produced 200 ton thrust solid rocket engine adopts multiple advanced technologies,
among which one is the most remarkable, which is the technology of large-diameter carbon fiber wrapped composite shell, marking that China has mastered the technology of
carbon fiber wrapped composite shell for large solid rocket engines.
A black carbon fiber "bundle" with a width of about 1 centimeter is stacked and wrapped layer by
layer on a specific device, and impregnated with special resin. After high-temperature curing, advanced heat treatment and surface treatment techniques are used to improve
the high temperature resistance and oxidation resistance of the carbon fiber shell, and the shell of
the rocket engine is preliminarily formed.
Using precision winding CNC machines to strictly control the winding speed and tension of carbon
fibers, ensuring that each layer of carbon fibers is tightly adhered to form a sturdy shell.
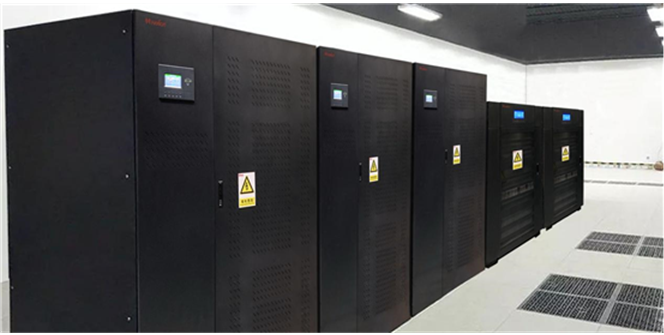
Highlights of this case's configuration:
The input and output are fully isolated, and the problems of sudden load, interference, and zero
ground are fundamentally solved. At the same time, the safety of equipment and personnel is also
guaranteed at a high level.
Strong impact resistance and strong adaptability to inductive loads that repeatedly start and stop.
The overload capacity has been significantly improved, running at 200% load for 10 minutes.
The protection level reaches IP54, with super strong environmental adaptability, such as high
temperature (below 65 ℃), high humidity, dust, vibration, etc.
Internal components are dust-proof treated, and a three proof paint process is used to prevent acid
and alkali corrosion, improving product reliability.
All internal components have undergone special anti grease treatment, further improving their
adaptability to the on-site environment.
Modular structure, with components placed in sealed devices for easy and quick maintenance.
After authorization, multiple parameters are adjustable and highly controllable.
● Adjustable speed intelligent fan, with high air volume and natural wind speed, easy to replace.
Perfect high-frequency mute technology, worry free working environment.
The input power factor is as high as 95%, which is energy-saving and efficient, greatly saving users'
usage costs.
Ultra high precision output: rated value accuracy < ± 0.5V; The instantaneous change value of
equipment start stop is less than ± 2V, and the response recovery time is less than 2ms.